Autonomous Forklift Tracking with WISER Systems
Mar 25, 2021 Autonomous vehicle market is expected to be a US$50bn opportunity by 2040, and all vehicles will have Level 2 autonomy by 2039, according to Lux Research’s report: 'Autonomous Vehicle Market Forecast: Demystifying the $50 Billion Opportunity' The report forecasts the adoption of AVs, including. Autonomous forklifts are lift trucks that work without human help. Autonomous forklift as the name stipulates is completely autonomous in nature. They are capable of doing all warehouses operations independently. Autonomous forklifts eliminate the need for human workers for warehouse operations. We've developed a breakthrough in machine learning, computer vision and robotic material manipulation. We call it shared autonomy. We're building the world's most advanced autonomous forklift - revolutionary increases in safety, efficiency, and throughput. Elevate your decision making and optimize your surface mining operation with a Komatsu FrontRunner Autonomous Haulage System (AHS) Mine-wide optimization and safety is your priority, and to help you continue to meet your bottom line while achieving zero-harm, our focus has been developing and improving autonomous mining solutions for nearly three decades.
WISER’s asset tracking and real-time location system (RTLS) enhances efficiency and safety by locating and tracking forklifts, pallet jacks, lift trucks, and buggies used to move valuable or dangerous assets. Keeping a real-time map of asset locations helps site managers manage key inventory and verify that it’s stored properly.
THE PROBLEM: DELAYS AND INJURIES
Forklifts expedite countless industrial processes, but they’re also involved in nearly 100,000 injuries per year in the U.S. alone. This does not account for other costly accidents, such as instances where forklifts inadvertently damage assets like pallets of product, industrial machinery, or other vehicles.

It’s also common for forklifts to go missing on large sites. This can create huge delays in task completion, even when other forklifts are available. Furthermore, it’s expensive to store and maintain forklifts to regulatory standards. While some are constantly in-use, many forklifts go unused for long periods of time, and it’s challenging to predict how machine demand.
All these issues translate into high costs in time, money, and brand trust. Similarly, site managers can drive high returns by knowing just a few simple pieces of data: Where each forklift is, where it has been, and how long it spends in each location.
THE SOLUTION: WISER’S ASSET TRACKING AND MICRO-LOCATION SYSTEM
Forklifts and other machinery are equipped with WISER UWB asset tracking tags. WISER’s Locator system calculates these tags’ real-time locations around the clock, reporting high-precision coordinate data overlaid on a floorplan or a facility map. This allows site managers to locate any tagged piece of machinery at any time, whether the machine is unmanned, unpowered, motionless, or in-transit.
It’s also useful to attach tracking tags to other objects like pallets or crates of product, or to give body-worn tags to employees working in proximity to heavy machinery. For instance, by tagging specific pallets of product it’s possible to eliminate the need for manual searching either before or after transit. This also cuts out the need to update inventory mid-process, since a pallet’s location will update autonomously as it moves across the floor.
Autonomous Forklift Cost
WISER’s RTLS solution can also utilize customized alerts based on perimeter breach or other spatial and temporal settings. These alerts can be used to prevent machine-machine collisions, like when multiple forklifts cross similar paths. By giving tracking tags to personnel, end-users can also help prevent machine-worker collisions.
THE RESULTS: SAFER CONDITIONS AND REDUCED DOWNTIME
This use of WISER’s UWB localization system generates an immediate, accurate, and always-current picture of forklift locations and movement histories. It shows not just where and when each forklift is used, but frequency of use over time. This allows site managers to quantify the use of and need for their machinery, seeing whether workers or timely projects are delayed by lack of equipment. It also helps managers assess whether they have too many forklifts on-site and might want to liquidate some of them.
WISER’s high levels of precision show exactly where tagged forklifts do and do not move. This can be compared side-by-side with tracking histories for employees, displaying how routes taken and work processes overlap or intertwine.
WISER’s Locator also helps ensure that forklift operators never pick up the wrong pallet, or that any error will be flagged instantaneously—long before a mistake becomes costly. Furthermore, WISER’s immediate, precise location of both the forklift and the product to be moved can increase success rates for timely projects, like perishable or expedited goods needing to be found and moved quickly to keep to a delivery schedule.
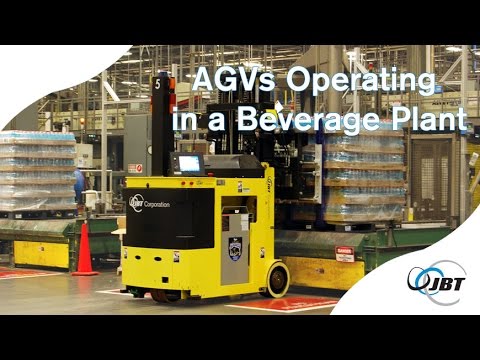
Autonomous Forklift Manufacturers
Ultimately, this helps reduce unnecessary costs, like time spent manually hunting for misplaced vehicles or the expense of storing and maintaining unneeded forklifts. This system helps ensure that no vehicle will be lost or forgotten at odd corners of a warehouse or factory.
Autonomous Trucks On The Road
Most importantly, WISER’s system helps make a safer working environment wherever forklifts are used.
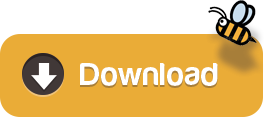